Backflow valves are everywhere!
Backflow is the reversal of the flow of water from any source of contamination back to the potable (or clean) water supply. Consider having a hose from a garden or garage in a bucket of soapy water, and having a backflow event occur causing that soapy water to “backflow” into the drinking water portion of your home and possibly neighborhood. You can check state and other local administrative codes or other regulation on the correct backflow to use as there are various types of backflow preventers that exist for different applications and health hazard conditions. The most common are double check backflow preventer valves and reduced pressure backflow preventers. Backflow preventers are primarily used in sprinkler, irrigation, chemical waste, wastewater, sewer, and residential backflow preventer backflow applications.
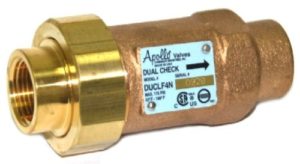
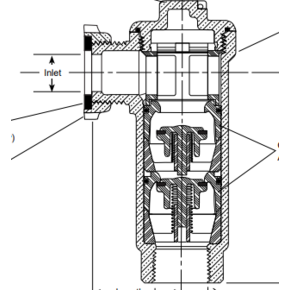
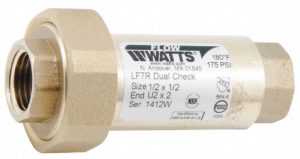
Dual Check Valves – The Dual Check Valve or double backflow prevention valve is basically a simplified Double Check Valve without test cocks and shut off valves. They aren’t testable and are generally used by water companies and installed after a water meter to prevent the meter from running backwards and offers a very low protection against actual backflow events. This type of device is the center of controversy with many backflow authorities and should never be confused with Double Check Valves. Check with local authorities for required installation, as most do not recognize these as backflow prevention devices.
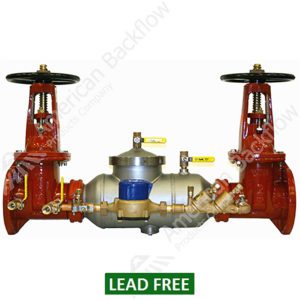
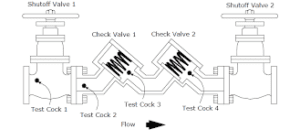
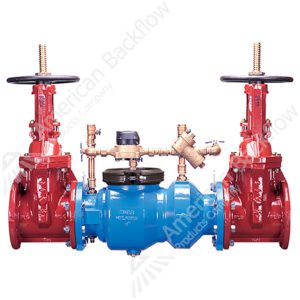
Double Check Valves consists of two check valves assembled in series. This uses two operating principles: first, one check valve will still be able to act, even if the other is jammed wide open. Secondly the closure or failure of one valve reduces the pressure differential across the other, allowing for a more reliable seal, and avoiding major leakage.
Smaller valves can be as small as 1/4″ in diameter and may be so compact that they are barely noticeable particularly when they are integrated into the bodies of existing taps (faucets). Larger check valves can commonly be as big as 12″ diameter and may be installed with ball valves at the ends, for isolation and testing. Often, test cocks, smaller ball valves, are in place for attaching gauges and other test equipment for evaluating the pressure of each chamber to see whether the double check assembly is still functional.
Double check valve assemblies are suitable for prevention of back pressure and back siphonage. It is commonly used on lawn irrigation, fire sprinkler and combi-boiler systems. If the hazard is higher, even a relatively low hazard such as using antifreeze in the fire sprinkler system or the usage of chemicals and cleaning of tanks, then a reduced pressure zone device which is a more reliable check valve may be needed.
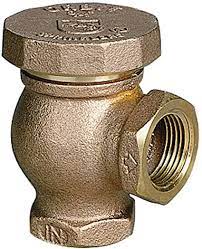
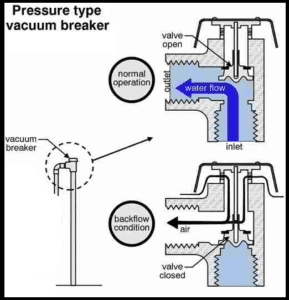
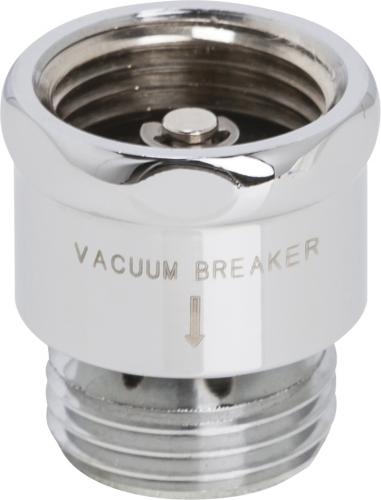
Atmospheric Vacuum Breaker – The atmospheric vacuum breaker is one of the cheaper, more accessible backflow prevention assembly. The AVB is a non-testable unit and are good for back siphonage only for non-health hazard or health hazard conditions. Think garden hoses or a faucet. They must be installed downstream from any shut off valves and cannot be under pressure for more than 12 hours. If you are using an AVB in backflow prevention on a irrigation system they must installed after every valve for each zone in the system. AVB’s must also be installed 6 or more inches (150 mm) higher than the highest water outlet in the system. Some municipalities do not allow the use of GFAVB’s as these units will NOT prevent a cross connection when there is backflow pressure and can only protect against water siphoning back into your main line.
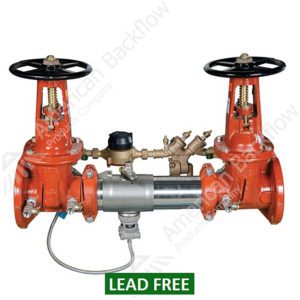
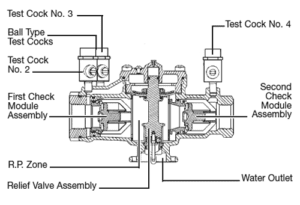
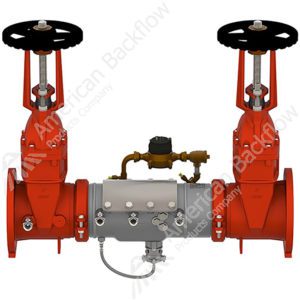
Reduced Pressure Zone Device – A RPZD is what is considered the minimum/standard for significant hazard applications. This is where the result of backflow to the main water supply could cause significant harm, whereas not for the highest of risks, such as human waste. They are considered standard because they prevent both back pressure and back-siphonage from occurring, because of a redundant design. Even with two check valves broken, the device will still provide protection, and because they are testable to ensure correct operation.
The device consists of two separate check valves, plumbed in series, with a pressure sensitive chamber in between. The chamber is maintained at a pressure that is lower than the water supply, but high enough to be useful downstream. The reduced pressure is guaranteed by a differential pressure relief valve, which will automatically relieve extra pressure in the chamber by discharging through to a drain. Four test cocks are installed to allow an inspector to verify proper operation of the valve with a differential pressure meter. Two valves (one before and one after the RPZD) are provided to allow for testing and repair.
To maintain constant operation and protection while being tested or repaired, facilities that require and RPZD must install two in parallel so that one device will be available at all times.